


.jpg)

 |
Tischmesserschmied |
"Alle Handwerke der Schmiede, der Herder und Schleiffer,
der Feger, der Metzmacher sind zugleich uff das Metzmachen privilegiert
und mögen ohne Unterschied sich des Metzmachens gebrauchen." so
niedergeschrieben 1619 um zu begründen, dass der Beruf "freigegeben"
werden sollte für alle Solinger Handwerker, da das Schwertschmieden
alleine nicht ausreichen konnte, die Menge der seinerzeit schon
vorhandenen Handwerker zu nähren. So gesehen ist die Basis des Solinger
Weltruhms, die Qualität der Tischmesser, eher Not denn Tugend.
|
Das Buch erzählt aus der Arbeit der
Schleiferfamilie Hartkopf; hier hatten sich zur Zeit der Entstehung des
Werkes nicht nur Erinnerungen erhalten, sondern auch noch der Kotten und
manch alte Gerätschaften. Die seinerzeit "Alten" konnten aus ihrem
eigenen Berufsleben manch Detail dazu beitragen, ein beredtes und extrem
detailliertes Bild der Arbeit der Messerschmiede niederzuschreiben. Eine
Arbeit mit einem extrem hohen Grad an Authenzität und wahrlich ein
beachtenswertes Dokument. |
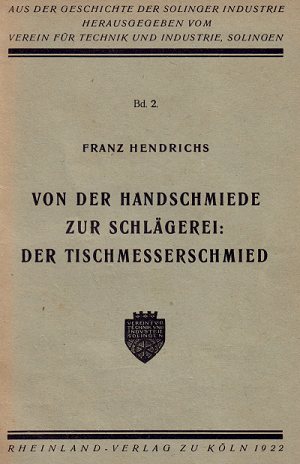 |
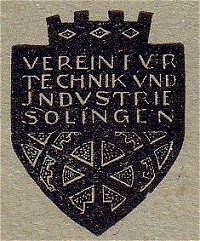
Schwarzweiß-Zeichnungen: Carl Hartkopf jr.
Fotos: Paul Weyerstahl, Solingen
Druck: Paul Gehly, Köln
Rheinland-Verlag, Köln, 1922 |
Messerschmiede spielen schon ausgangs des 15.
Jahrhundert. In den Privilegien der Schwertschmiede von 1472 findet sich
ein Abschnitt, der sagt, "dat ein jeglich Schmied
jeglichs Tages, als man schmieden mag, vier Schwert schmieden mag und nit
mehr ; und jeglich Metzschmied zehn Stechmetz ..." Bereits um 1571
waren die "Meßmacher" den Schwertschmieden in der Anzahl überlegen.
Das früher gewonnen Eisenerz bzw. die angelieferten
Stahlsorten konnten nicht immer so, wie sie waren, zum Schmieden von
Messern benutzt werden. Die Härte bzw. Sprödigkeit musst durch Mischen,
das sog. "Gärben", ausgeglichen werden, wobei es bei diesen Glühvorgängen
auf großes Wissen und Geschicklichkeit beidermaßen ankam.
Gearbeitet wurde in teilweise abenteuerlich
anmutenden, weil über die Zeit zerfallenen Kotten, wie hier dem
Wertherhammer, unweit Schulkohlfurt an der Wupper. |
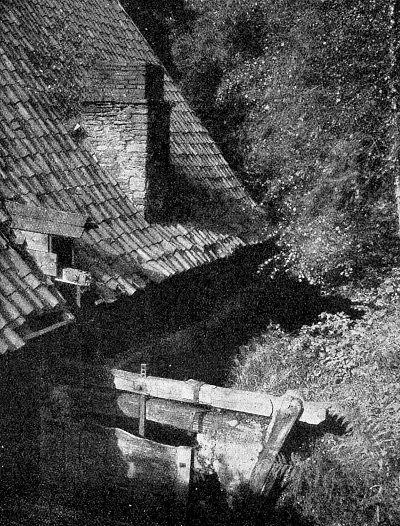 |
Der Stahl, auf den sich Solinger qualitätsweltruf
früher gründete, kam aus dem Siegerland; hier fanden sich besonders reine
Eisenerze. Auch war dort genügend Holz, um den Stahl zu "kochen" und
neben der daraus gewonnenen Holzkohle gab es zum Glück auch noch
Steinkohle. Beides, Erz wie Kohle, wurde in sehr geringem Maße auch einst
auf Solinger gebiet geschürft, doch weder Menge noch Qualität waren von
Bedeutung. Also blieb nur, das schwere Zeugs per Pferdewagen aus dem
Siegerland nach Solingen (und Remscheid) zu schaffen. Beide kleinen
Flüsse, die Sieg wie die Wupper, waren, obwohl über den Rhein verbunden,
nie für Lastkähne schiffbar. |
Ein Blick in das Innere des Hammers, also der Werkstatt.
Schmied war ein Zunftberuf, dessen Regularien
vorsahen, "Niemand soll auch von den
vorgeschriebenen Werkleuten fremden Menschen dat Ambacht not das Werk
lehren, dann als einn ehelichen Kindern." (Ambacht = Handwerk)
Die Lehre dauerte übrigens 6 Jahre.
Tischmesser wurden erst "zu Hofe" und bei "feinen
Leuten" im 16. Jahrhundert Mode. Weniger als individuelles Messer für
jeden, der tafelte, als vielmehr als Vorlegemesser oder größeres
allgemeines Messer auf dem Tisch, mit dem sich jeder "seine Scheibe
abschneiden konnte" - wie das Sprichwort weitergetragen hat.
|
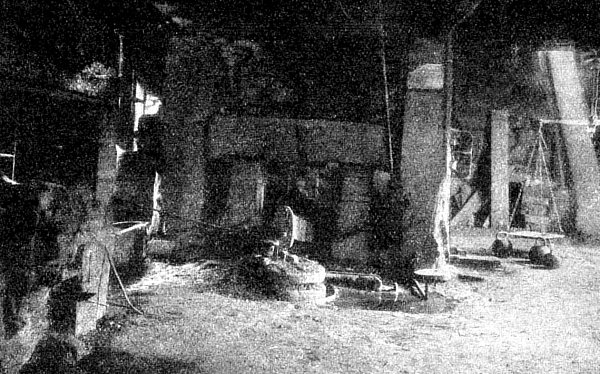
Deutlich ist der Reckhammer zu sehen, dessen Gewicht nur durch
nichtmenschliche Kraft, nämlich die des Wassers, bewegt werden konnte.
Der Hammer existierte lau einer Kaufurkunde bereit vor 1694.
|
Um 1800 waren in Solingen insgesamt rund 4.000
Arbeiter in der Klingenindustrie beschäftigt. Rund 1.200 Messerschmiede,
ca. 1.000 Schwertschmiede, etwa 800 Schleifer, gut 400 Scherenmacher.
Scharfhausen, mdtl. "Scharpes", auf Hästen zu, ist
eine kleine Ortschaft, in der Mitte des 19. Jahrhunderts (und früher)
etliche Messermacher arbeiteten, u. a. die Familien Spitzer, Willms,
Röttgen, Löhmer und Hartkopf.
In dieser Hofschaft war die Alte Schmiede der
Hartkopfs zu finden; ein Gebäude bescheidener Dimension, aber typisch für
die ganze Stadt.
Das Einkommen aus der Arbeit reichte meist nicht,
um den Lebensunterhalt vollständig zu finanzieren. Deshalb hielten sich
solche Haushalte auch noch Vieh; berichtet wird beispielsweise, dass die
Familie Hartkopf um 1830 vier Schweine, zwei Kühe und ein Pferd besaß. |
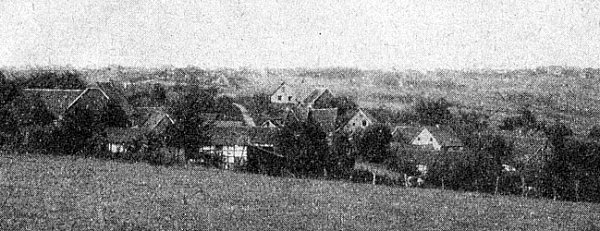
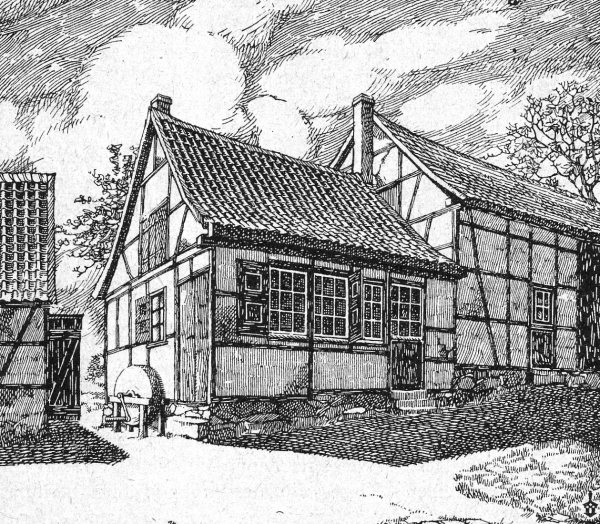
|
Schritt für Schritt Handarbeit. Heute unbezahlbar,
damals gar nicht anders möglich. Gerade um die ganzen Partien der Messer
gleichmäßig zu fertigen, bedurfte es einer intensiven Erfahrung und hohen
Konzentration bei der Arbeit, auch wenn diese noch so stupide zu sein
schien. Was sie aber nicht war, denn es war ja nicht nur die Fertigung
der Messer, die der Meister und seine Gehilfen zu besorgen hatten,
sondern auch alles andere "Drumherum": Vom Herrichten und Instandhalten
der Werkzeuge und des Raumes, dem Zu- und Vorbereiten des Eisens bzw. des
Stahls, dem Transport der Waren und schließlich auch noch der Kontakt zu
anderen der Zunft und Kenntnis in nicht weniger Gesetzen, Vorschriften
und Verpflichtungen, als sie heute existieren (na ja, ein paar weniger
schon).
|
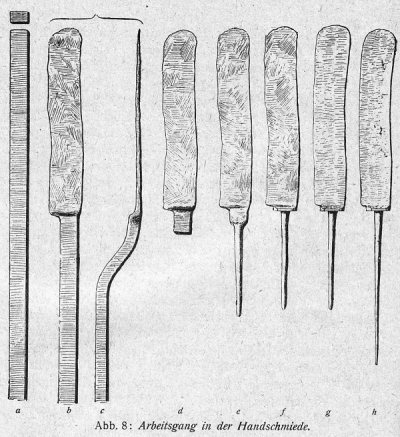 |
|
Zum Schmieden gehörten zwei, der Darhalter und der
Afhäuer. Der Afhäuer (rechts) war die Hilfe für den Schmied. Der Afhäuer
gab drei oder vier kräftige Schläge mit seinem schweren Hammer, der
Stuckhacke, auf die falsche Seite des Stahles, während der Schmied die
Hette hin und her wandte, um zwischen den Schlägen des Afhäuers mit
seinem leichten Hammer auf die hohe Kante des Schmiedestückes zu
schlagen. Zum Schluss, "beim letzten Zug", hämmerten beide nur noch auf
die flache Seite. |
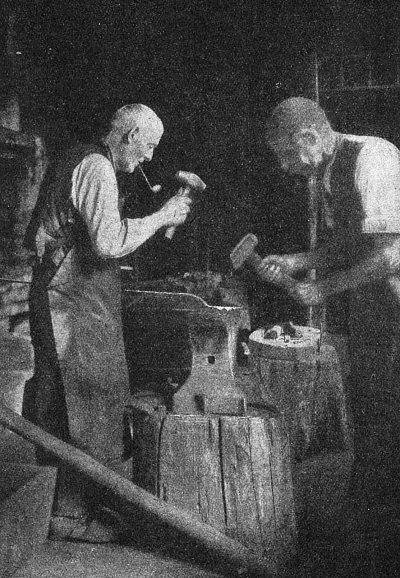 |
|
|
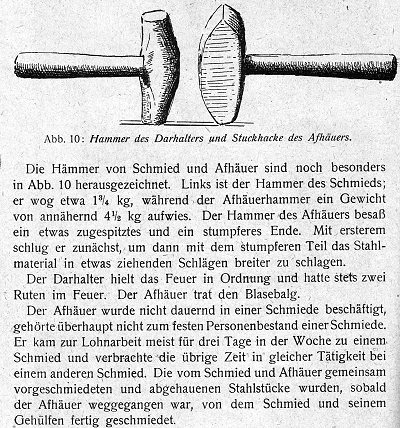 |
|
Besonders anstrengend war das Opdiwen; hier ging es
darum zwischen der Klinge und dem später mit dem Heft (Griffschale, meist
Holz, oft auch Metall) verbundenen Erl (der spitze Stift hinter dem
Messer) einen Wulst zu schlagen; gewissermaßen das "dicke Ende" des
Messers. Damit konnte dann das Heft, der Griff, besser fixiert werden und
zugleich war es ein Griffschutz, damit niemand an der scharfen Kante
abglitt, wenn er das Messer in der ("flutschigen") Hand hielt. Die
Klemmvorrichtung, in der das Messer gesteckt wurde, damit es so
bearbeitet werden konnte, heißt Prahm; der Hammer, mit dem der Schmied
auf die Opdiwers Pipe schlägt, wiegt um die 4 kg. |
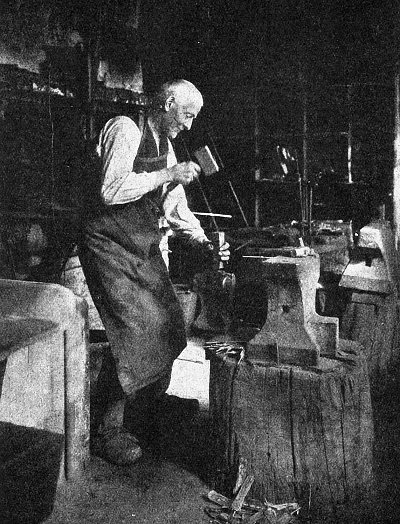 |
|
|
|
|
|
|
|
.jpg) |
|
|